Understanding Air Powered Vacuum Pumps

Ever wondered how some machines create suction without electricity? The answer often lies in the ingenuity of air powered vacuum pumps. These devices, relying on the power of compressed air, offer a simple yet effective way to generate vacuum for a multitude of applications.
At its core, an air powered vacuum pump harnesses the flow of compressed air to evacuate air from a designated chamber, thereby creating a pressure difference. This pressure differential is what we call vacuum. This seemingly basic principle unlocks a wide range of possibilities, from lifting and holding objects in automated manufacturing processes to evacuating air from packaging for prolonged shelf life.
The functioning of these pumps revolves around a venturi effect, created using a specifically designed nozzle within the pump. Compressed air is forced through this nozzle at high velocity, creating a low-pressure area at the vacuum port. This low-pressure region then draws air from the target area, effectively creating a vacuum.
Understanding the workings of these pumps is crucial for selecting the right tool for the job. Factors like the required vacuum level, the volume of air to be evacuated, and the available compressed air pressure all play a role in determining the optimal pump configuration.
The simplicity and robustness of air powered vacuum pumps make them a popular choice across various industries. Their ability to operate without electricity also makes them suitable for hazardous environments where electrical sparks pose a risk.
While the precise origins of air powered vacuum pumps remain somewhat obscure, their development is closely tied to the advancements in compressed air technology in the late 19th and early 20th centuries. The increasing availability of compressed air systems in industrial settings paved the way for the widespread adoption of these versatile vacuum generators.
One common issue with air-powered vacuum pumps is maintaining a consistent vacuum level. Fluctuations in the compressed air supply can directly impact the pump's performance. Proper filtration and regulation of the compressed air are essential for optimal operation.
Benefits of Air Powered Vacuum Pumps:
1. Safety in Hazardous Environments: The absence of electrical components minimizes the risk of sparks, making them ideal for flammable or explosive environments.
2. Simplicity and Reliability: The relatively simple design of these pumps translates to robust performance and reduced maintenance requirements.
3. Portability: Many air powered vacuum pumps are compact and lightweight, allowing for easy transportation and deployment in various locations.
Best Practices:
1. Regular Maintenance: Inspect and clean the pump regularly to prevent debris buildup and ensure optimal performance.
2. Proper Air Filtration: Install an air filter upstream of the pump to remove contaminants that can damage the internal components.
3. Correct Sizing: Select a pump with the appropriate capacity for the intended application to avoid performance issues.
4. Leak Detection: Regularly check for leaks in the vacuum system to maintain optimal vacuum levels.
5. Monitor Compressed Air Supply: Ensure a consistent and adequate supply of compressed air to prevent fluctuations in vacuum performance.
Challenges and Solutions:
1. Low Vacuum Level: Check for leaks in the system or insufficient compressed air supply.
2. Excessive Noise: Install a muffler or silencer to reduce noise levels.
3. Freezing: Use a moisture trap in the compressed air line to prevent freezing in cold environments.
4. Pump Overheating: Ensure adequate airflow around the pump to prevent overheating.
5. Short Pump Lifespan: Regular maintenance and proper lubrication can extend the pump's lifespan.
FAQ:
1. What is an air powered vacuum pump? An air powered vacuum pump uses compressed air to generate vacuum.
2. How does it work? It uses the venturi effect to create a low-pressure area.
3. What are the applications? They are used in various industries, from packaging to automation.
4. What are the advantages? They are safe, reliable, and portable.
5. What are the disadvantages? They can be noisy and require a compressed air source.
6. How do I maintain it? Regular cleaning and inspection are essential.
7. How do I choose the right pump? Consider the required vacuum level and air volume.
8. Where can I learn more? Consult manufacturer websites and technical manuals.
Tips and Tricks: Regularly drain moisture from the air supply. Use appropriate fittings and tubing to prevent leaks.
In conclusion, understanding the mechanics of air powered vacuum pumps unlocks their potential for a variety of applications. Their simplicity, reliability, and safety features make them invaluable tools across various industries. From automated manufacturing processes to packaging and material handling, these pumps play a crucial role in enhancing efficiency and productivity. By understanding the principles of operation, maintenance requirements, and troubleshooting techniques, users can maximize the benefits of these versatile tools. Further exploration through manufacturer resources and technical manuals can provide a deeper understanding of specific pump models and their optimal application. Embracing these tools empowers businesses and individuals to leverage the power of vacuum technology in a safe, efficient, and cost-effective manner.
Had ridden unlocking the past perfect of riding
Unlocking the secrets your guide to fantasy tower defense codes
Unlocking jefferson county ny your guide to career success
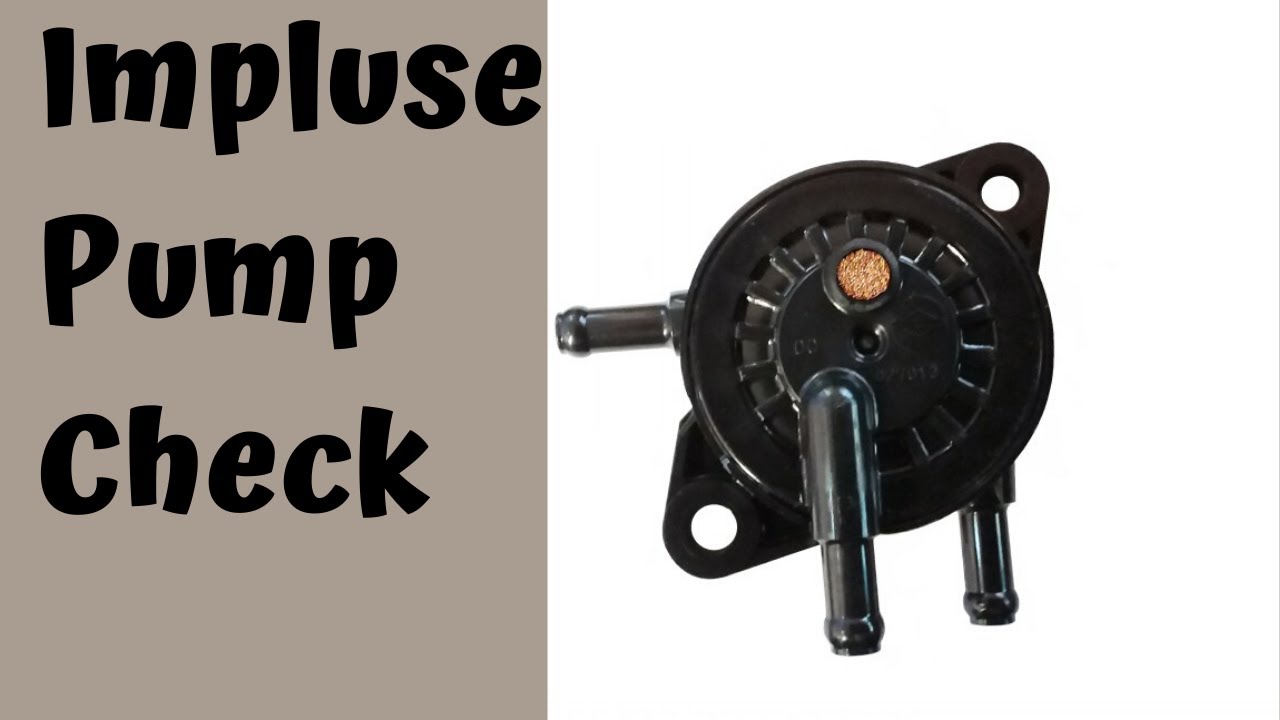










